Еще буквально пару десятилетий назад слово «лазер» прочно ассоциировалось с
Наиболее распространенное применение в станкостроении процесс лазерной обработки нашел в раскрое листовых материалов и различных тонкостенных профилей. В нашем случае нас интересует непосредственно раскрой и обработка металлических изделий.
Лазерный раскрой металла на данный момент является практически самым дешевым способом резки металла за единицу длины, уступая только резке на гильотинных ножницах, но при этом значительно превосходя гильотины по функциональным возможностям.
Конструкция лазерного станка для резки металла
В самом базовом случае станок лазерного раскроя представляет координатную систему с тремя взаимно перпендикулярными осями. Модификации могут быть различными, но доминирующей является компоновка с неподвижным столом и перемещающимся по нему порталом, на котором закреплена режущая голова. А уже эти координатные системы могут быть доукомплектованы огромным количеством средств автоматизации и иметь практически любые размеры.
Процесс перемещения режущей головки, а также процесс резки контролируется ЧПУ. Интерфейс оператора в современных стойках позволяет контролировать все необходимые параметры раскроя, которые могут быть внесены как вручную, так и рассчитаны полностью автоматически. Перечислять все возможности современных ЧПУ просто не представляется возможным — они огромны — начиная с автоматической раскладки деталей на листе и заканчивая полноценным
Оптоволоконный лазерный станок для резки металла
Ключевым компонентом комплекса лазерного раскроя является непосредственно сам источник лазерного излучения или «резонатор». Самыми распространенными типами источников, используемых в промышленности, являются оптоволоконный лазер и СО2 лазер, который иногда называют газовым. Практически безусловным выбором в настоящее время для резки металла является оптоволоконный тип лазера. Он имеет гораздо более низкую длину волны и за счет этого металлы, которые отлично абсорбируют коротковолновое излучение, более эффективно режутся этим типом лазера. Если еще относительно недавно СО2 машины были более предпочтительны при резке толстых металлических листов, то сейчас с колоссальным удешевлением высокомощных оптоволоконных источников данное преимущество сведено на нет. При этом, если стоит задача резки цветных металлов, а в особенности меди, на данный момент вариантов использования
Не последнее значение занимает более высокая энергоэффективность волоконного источника. КПД «от розетки» может достигать 30%, тогда как для СО2 машин — это значение составляет не более 10%.
Как выбрать станок лазерной резки?
Для оптимального подбора базового лазерного станка необходимо учитывать не так много параметров.
Основные:
- максимальные габариты зоны обработки;
- максимальная толщина обрабатываемого материала;
- типы обрабатываемых материалов;
- толщина наиболее часто используемого в обработке материала;
- бюджет на станок.
Дополнительные:
- точность получаемой детали;
- серийность/партийность производимой продукции;
- количество рабочих смен;
- местные требования по трудовой безопасности.
С учетом грамотного подбора вышеуказанных параметров вероятность корректного выбора необходимого оборудования стремится к 100%. В случае необходимости увеличения производительности, дополнительной автоматизации оборудования, специализированных задач для станка лазерной резки специалисты группы компаний «ПроТехнологии» подробно проконсультируют по возможным опциям и нестандартным возможностям машин.
В завершении не стоит забывать, что спектр возможностей лазера сейчас не ограничен исключительно резкой листа. В данный момент ассортимент компании «ПроТехнологии», помимо непосредственно лазерных станков с ЧПУ, включает установки для резки трубы и профилей, машины для лазерной сварки, машины для лазерной резки, а также установки для лазерной наплавки.
В данном материале мы не учитывали много вопросов касательно процесса резки, такие как подбор рабочего газа, особенности конструкций режущих головок, типы двигателей и приводов, дымоудаление
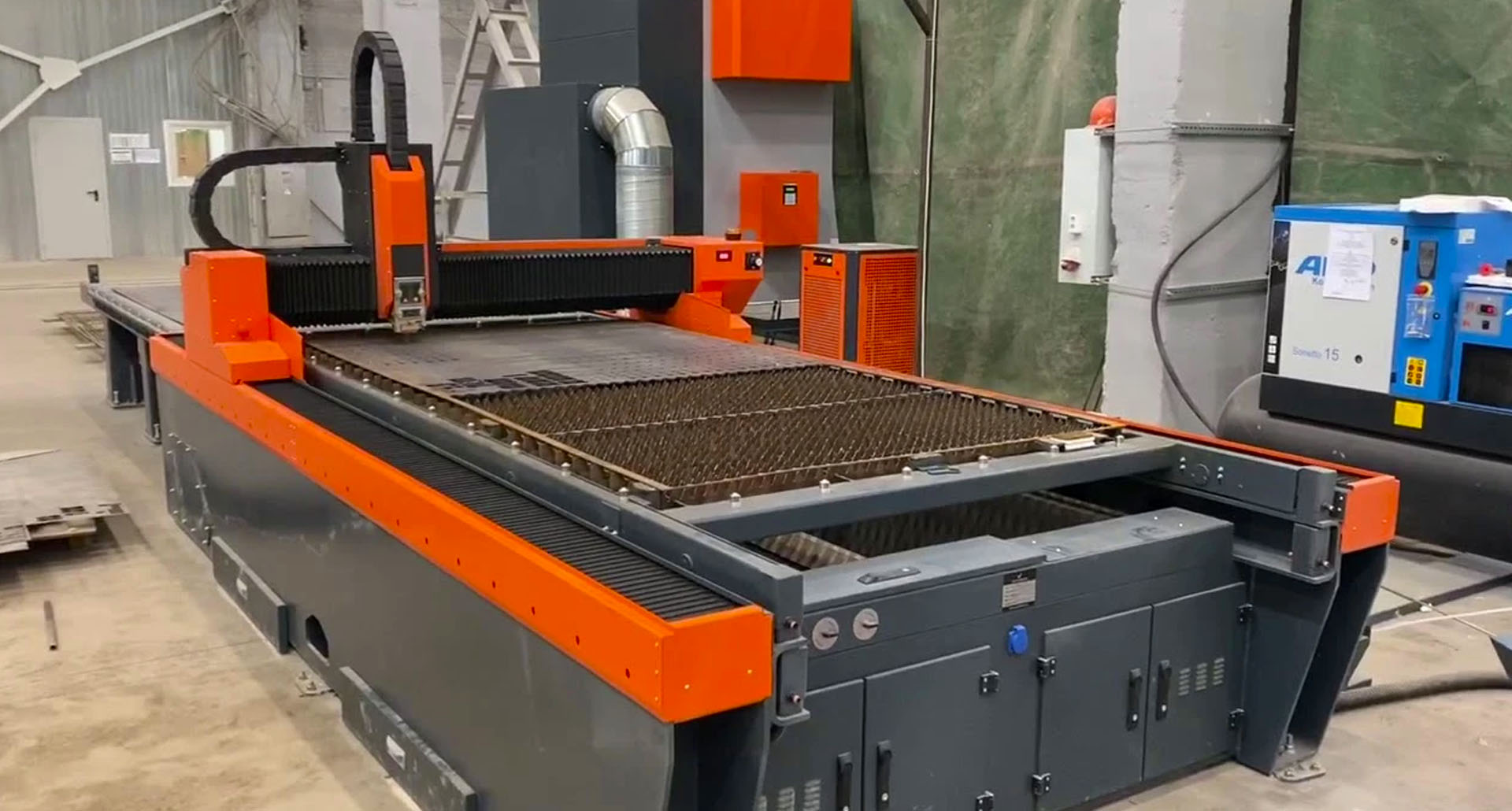
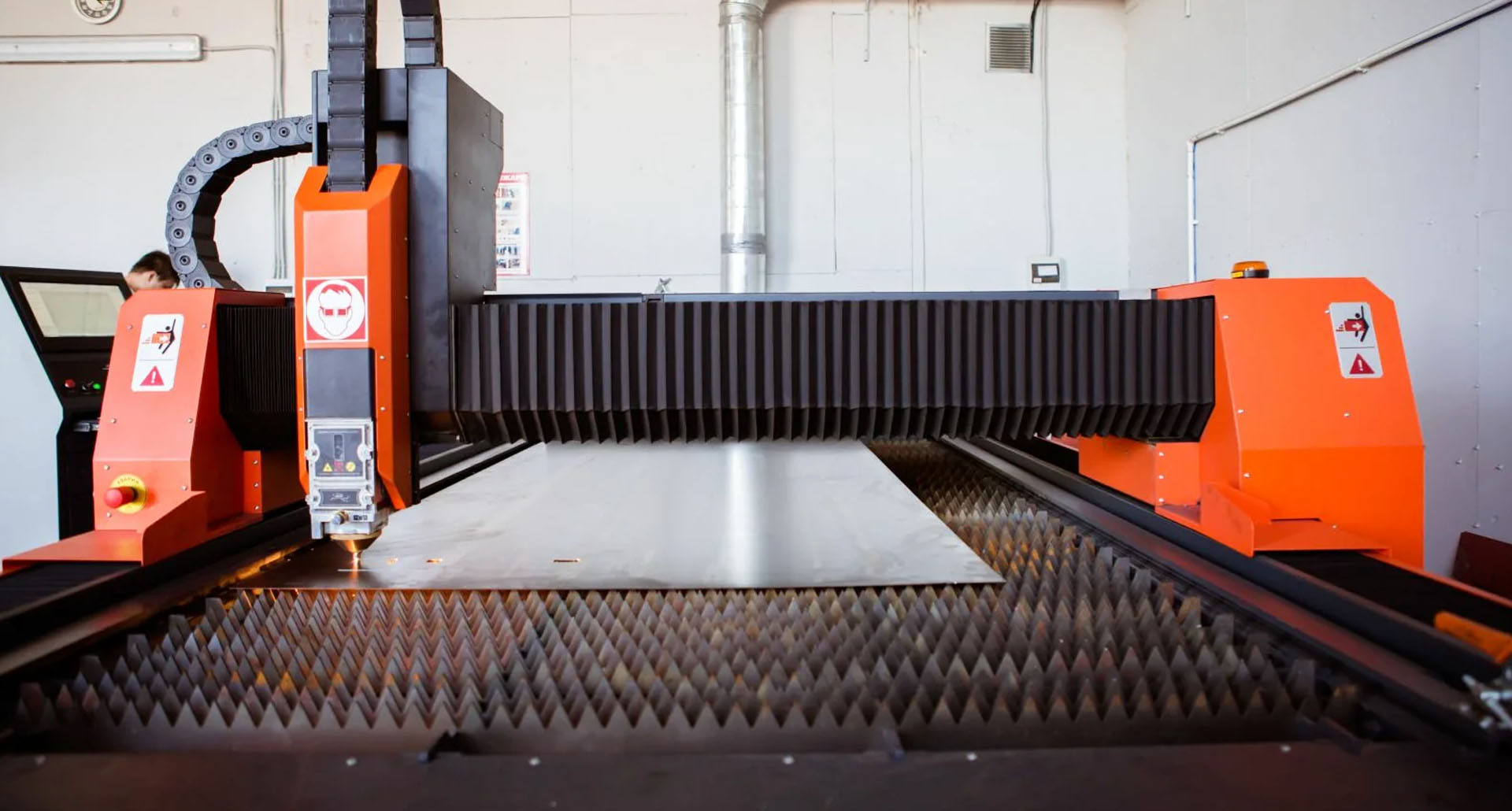
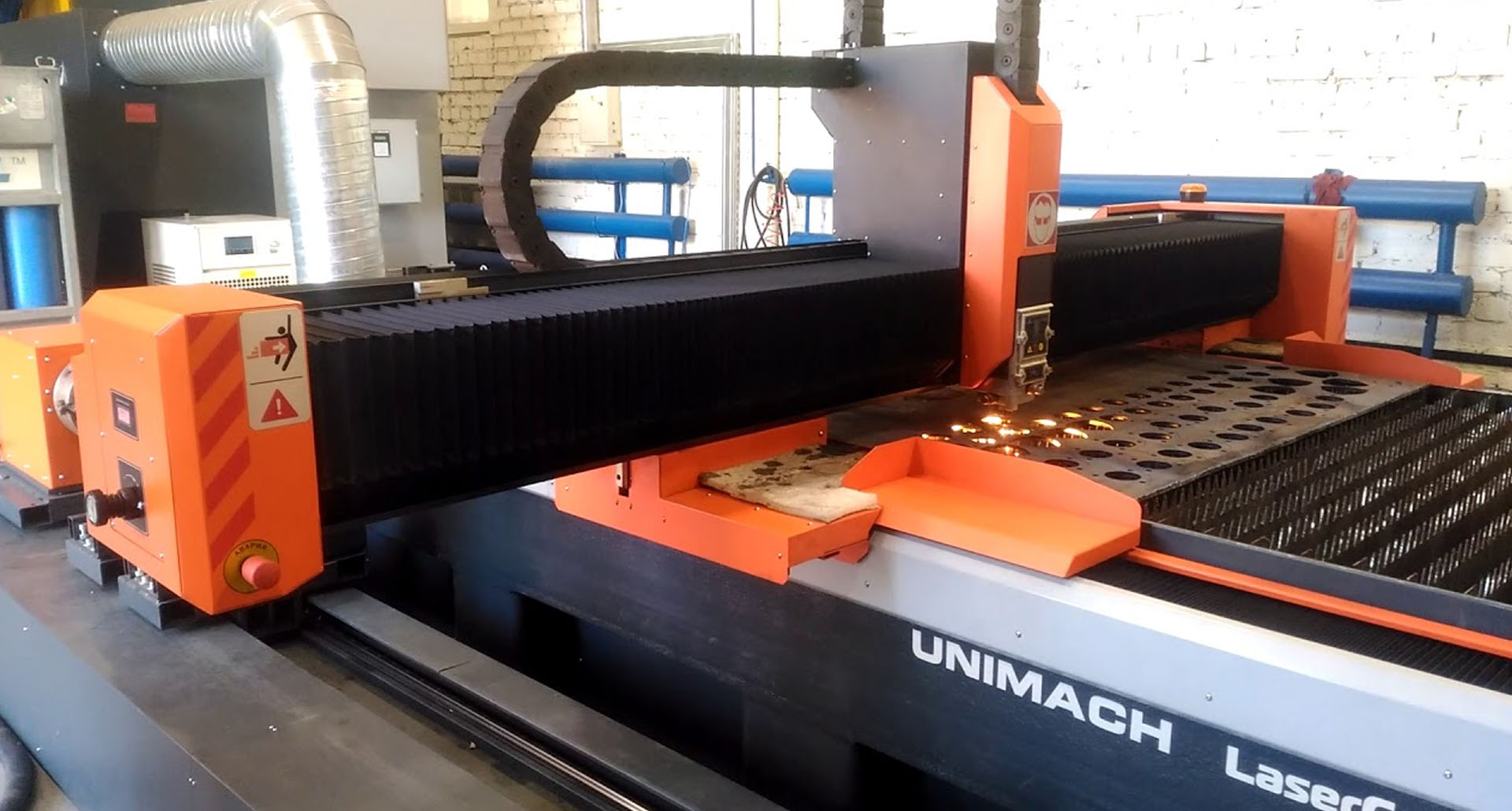
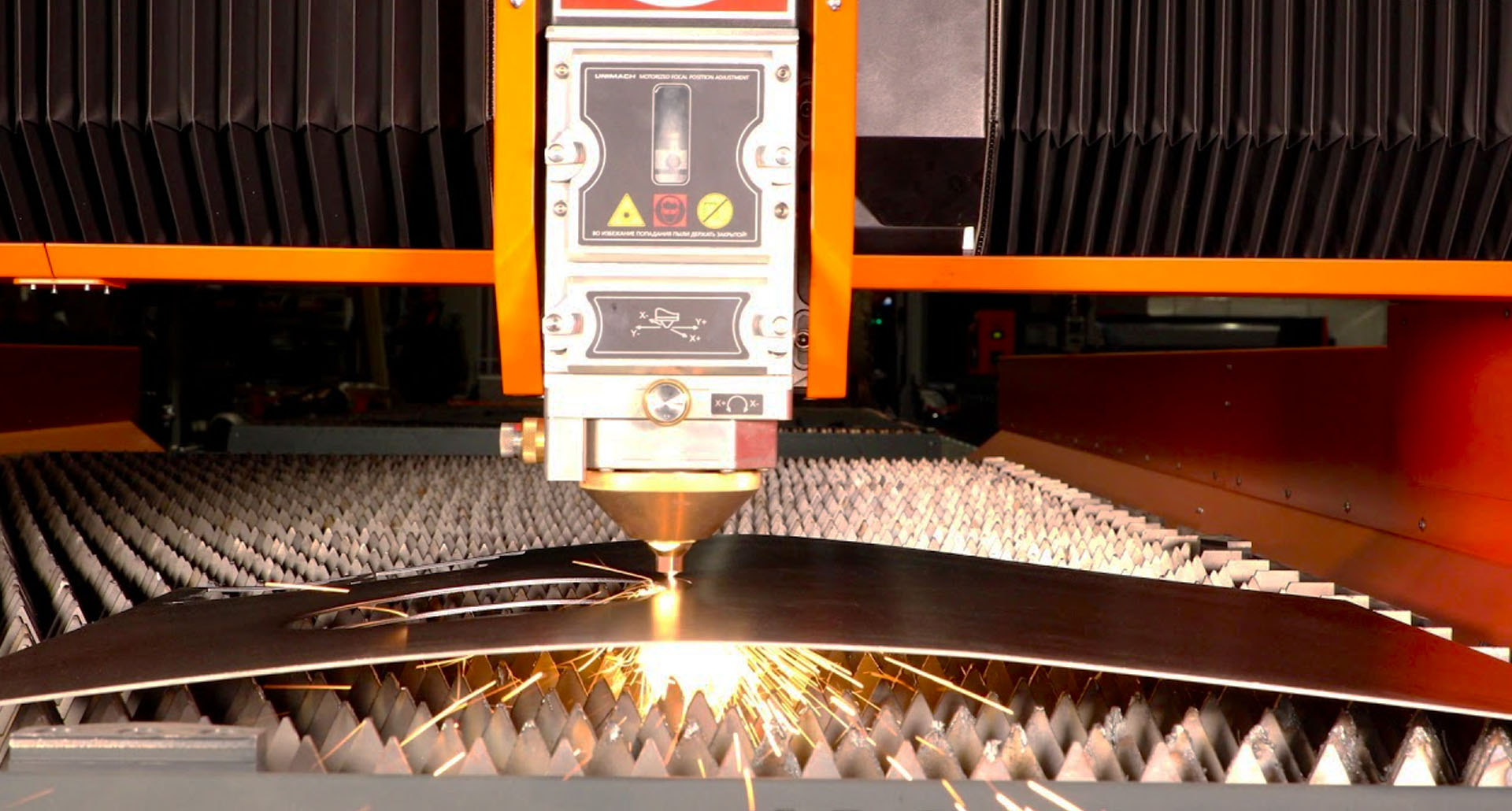